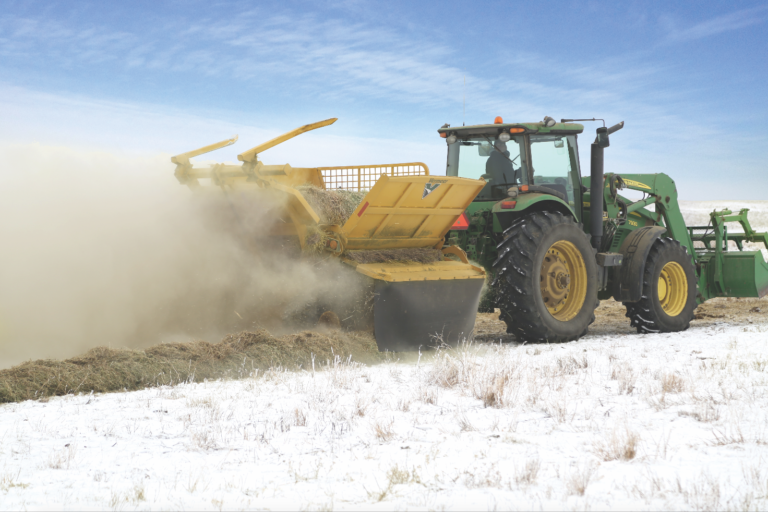
A Machine of Opportunity – Bale Processors Bring Versatility to the Farm and Beyond
December 2017
For many years, livestock producers have embraced the use of bale processors for a lot of different reasons. There are few studies that have evaluated them with a cost analysis to track the value they provide, but when you visit with owners and operators, one of the biggest reasons they prefer bale processors is the versatility the machine brings to their operation.
Finding Efficiencies
Most bale processors function like a Swiss army knife in terms of versatility. Owners can process everything from hay to cornstalk bales, and round bales to square bales. They get the flexibility to perform all kinds of tasks with a machine like the Vermeer BPX9000 — laying down windrows in the field, bunk feeding, creating hay material for total mixed rations (TMRs) and blowing bedding into barns or forage into storage bunkers. Other types of processors can even be used for different industries — for example, the Vermeer Catapult™ CPX9000 bale processor is designed to process round or square bales and accurately distribute material up to 100 ft (30 m). In an agricultural application, this is beneficial for livestock producers to be able to bed their livestock in covered buildings. In an industrial application, the CPX9000 can be used for land reclamation projects to distribute a consistent layer of straw helping to reduce erosion.
Improved Palatability
One of the biggest reasons why a livestock producer sees value in a bale processor is due to their ability to help turn marginal quality hay into a more palatable feed for livestock. Why? Processing hay helps effectively eliminate the dust, mold and mildew that accumulates over time in a bale before the hay enters the digestive system of the cows. Plus, hay processing reduces the amount of sorting, waste and manure that typically takes place around the bale ring.
Bale processors with multiple cutting stages (like the Vermeer Final Cut™ FPX9000 bale processor) can reduce the size of processed hay down to an average cut length of 1.25-4 inches giving producers the flexibility to process and then mix their own feed rations. According to University of Wisconsin Forage Agronomist Dr. Dan Undersander, this hay length is the optimal material size for digestibility and efficiency in the cow’s rumen.1 The bale processor will also enable you to produce a piece of your TMR feed or to process hay into feed bunks along with other grains or supplements.
Waste Not, Want Not
If you process hay on a daily basis (even if you are processing into a windrow in open range on the ground), you can limit intake and reduce hay loss. Bale processors allow operators to better control and monitor consumption. Processing and windrowing bales in the field can result in more hay consumed and less hay wasted. All your cows can get an equal opportunity at feeding time because they have greater access compared to feeding with bale rings or to simply unrolling them in the field.
Find the Perfect Processor
When selecting a bale processor for your operation, be sure it provides the versatility you need. There are currently two basic styles of bale processors and both feature a similar rotor design for processing the bale. The primary difference between the two is how the bale is handled and turned in the tub.
One style of processor uses a dual feed-roller design with staggered, adjustable rollers. In contrast, the most popular processor design incorporates a simpler slat-and-chain bed. This creates a more consistent, user-friendly system when feeding the bale because the slats are constantly in contact with some part of the bale. This design can also avoid or reduce the hassle of twine buildup, which is fairly common with the previously mentioned dual feed-roller concept.
Required horsepower is another crucial factor that farmers should always consider when comparing models. If the bale is sluggishly moving through the processor, it can drag the tractor down and bring production to a screeching halt. There’s nothing more frustrating than dealing with a plugged processor (particularly during winter months). You will find that processors built to handle sufficient horsepower tend to generate a more even and consistent feeding action to the rotor. This can equate to fewer performance issues and can require less fuel to operate.
Evaluate Your Needs
There is no one answer to the question, “Does a bale processor make sense for a livestock operation?” The needs of each operation vary, so it’s important to evaluate what you really want to accomplish. Look around your operation and consider the possibilities — then ask your dealer for a demonstration.
Resources
1. https://makinhay.dvlpsite.com/advantages-of-balers-equipped-with-a-pre-cutting-system