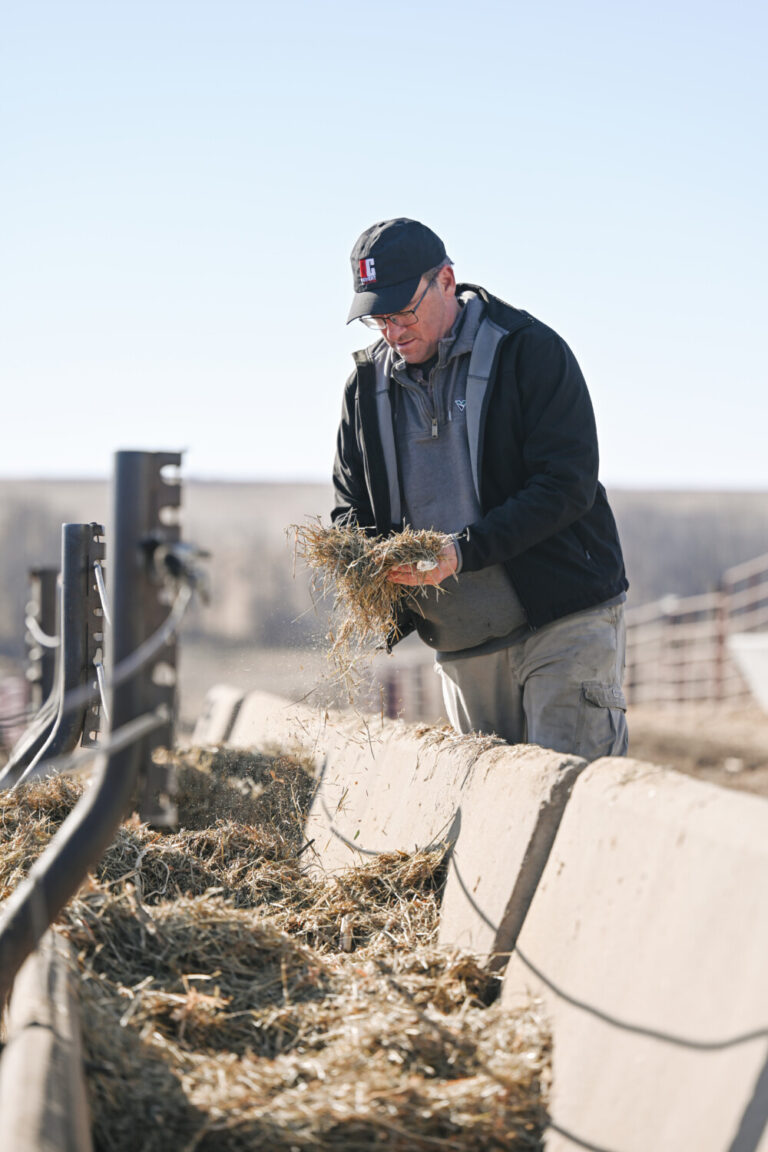
Lean Farm Management Helps Improve Vertical Mixer Efficiency
March 2023
What similarities exist between lean manufacturing and lean farming? Both concepts center around continuous improvement.
Lean manufacturing focuses on minimizing waste within manufacturing systems while simultaneously maximizing productivity. It is derived from the Japanese concept of kaizen, which attempts to change for the better through continuous improvement. Similarly, lean farming strives to minimize waste and increase efficiency. Lean is the concept of doing more with less resources.
Vermeer Executive Vice President and Chief Marketing Officer Mark Core helps drive lean manufacturing efforts that target waste and maximize efficiency.
“I have spent 26 years at Vermeer and have been heavily involved in our continuous improvement and lean kaizen efforts,” said Core.
His experience at Vermeer has taught him a number of lessons about lean management, which Core and his family incorporate on their family cattle operation.
Mark and his wife Deb have a multi-breed cow-calf operation focused on selling heifers to junior exhibitors and purebred operations around the country. Their operation, Boyert-Core Show Cattle, is a partnership with daughter Bailey and her husband Jared, along with Jared’s brothers who are based in Ohio.“We’re focused on providing great experiences for young people in the show cattle business. This extends beyond exhibiting to starting to build their own cow herds and perhaps inspire or create longevity in agriculture. That’s what inspires us,” said Core.
The operation continues to grow, due in part to a focus on continuous improvement through lean farming principles. Every time an improvement is made, it is time to take the next step. The process requires continuous change.
Small changes make big impact
Lean farm management addresses waste and increases productivity through incremental improvements to produce measurable results. Feeding cattle provides a great example. If you’re interested in practicing on your farm, start by carefully examining your feed handling practices. Are there ways you can reduce time and trips wasted moving material multiple times?
Core has implemented several different strategies over the years to introduce lean farming to their operation. From putting up hay to storing hay to feeding hay, changes in each of these stages have helped his operation gain efficiencies.
Incorporating baleage allows flexibility
One strategy is to examine harvesting practices. Core started using baleage to minimize waste. Baleage is hay that is too moist to store safely as dry hay, so it is wrapped in netwrap and then sealed in plastic.
“We are doing more baleage every year,” said Core. “It provides a window to harvest at the right time that works for us. It reduces dry matter loss at the time of raking or baling. It’s fun to open a bale that looks essentially like it did when you put it there six months ago.”
Proper storage minimizes waste
How you choose to store hay directly impacts potential loss. Storing bales in a hoop barn or wrapping dry bales is a best practice to minimize waste.
“Preservation of round bales has been a topic for 50 years, since they started being stored outside,” said Core. “Machinery, fuel and land costs have accelerated and created a strong desire to reduce feed waste. The investment is too high not to look at incremental improvements to reduce waste.”
Some producers store hay outside with little to no cover. Some producers will stack them next to each other, so the bales occupy less land. With this strategy, there is no chance for that product to breathe.
Beyond storage strategies, you can create waste when storing bales in inconvenient locations where they must be constantly moved.
“Sometimes you move a hay bale three, four or five times before you use it. Every one of those touches is a cost,” said Core.
Direct costs include equipment hours and fuel. There are also indirect costs associated with the time lost moving bales. The ideal situation with lean farm management is to move your feedstuffs once to the selected storage location and then transport them directly to the mixer with the least amount of travel time.
Vertical mixer adds efficiency
Six years ago, Core relied on bale rings to feed his cattle herd. He knew he could refine his feeding strategy to minimize waste. Inefficient feeding practices and improper feed storage can lead to significant losses and higher input costs.
Purchasing a Vermeer vertical mixer changed the game, further minimizing waste and allowing Core to continue the pursuit of lean farm management. However, lean farming should be viewed as a journey. There are limitations to how fast change can be implemented based on how current facilities are laid out or additional investments that need to be made.
For example, investing in a concrete mixing floor keeps feed stuffs out of the mud and the snow. Because the mixer sits on the concrete pad, materials that spill from the mixer can be quickly recovered instead of being lost in the mud.
If you’re working toward lean farming, you’ll want to optimize the distance between the feed ingredients and the mixer when planning and laying out the yard. This is an ongoing process, and even experienced producers like Core can find room for improvement.
“If any of us farmers could observe from above (a drone), and take the emotion out of it, we would see waste that you would not while working in the moment,” said Core.
Manufacturing plants often times use spaghetti charting with stopwatches and clipboards to measure motion and identify excess motion that can be removed. The goal is to minimize unnecessary motion and thus increase efficiency. This same approach applies to the feed mixing process.
The tractor burns more fuel traveling between the ingredients and the mixer when the distances have not been optimized. Cutting unproductive travel to transport feedstuffs to the mixer also gives more time for other critical tasks, especially during calving season.
You can eliminate a lot of wasted time and maximize time spent mixing by optimizing travel distance to feed stuffs, selecting the right mixer and properly layering products.
“You can easily collapse a three-hour process into a two-hour process. That is a big deal when you have a short time window,” said Core.
Set up for success
When preparing the mixing system, start with the proper loading tool. Larger skid-steer loaders offer several advantages for loading a mixer. A good operator can quickly switch from a bucket to forks to accommodate different feed stuffs.
Producers who already own high-horsepower skid steers often want to load the mixer without having to bring in a tractor that burns additional fuel. However, skid-steer loaders have limited reach. A low-profile mixer, a concrete wall or a low-cost ramp are feasible alternatives. A twin-screw mixer offers lower sidewalls than a large single-screw mixer.
Core initially built a low-cost ramp using concrete blocks to help a mid-size skid-steer loader feed the mixer. This loading system evolved as feed demand increased. A tractor now loads feed stuffs into a large capacity Vermeer vertical mixer.
Once you select the proper loading system, determine the best method for mixing the rations.
“There’s an art to understanding what goes into the mixer first,” says Core.
The goal is to achieve the quickest and most effective mix time. Starting with light, fluffy crops like hay will offer a different mix time than if you start with heavy silage bales. You can experiment and make adjustments over time — or reach out to a Vermeer dealer or a mixer company for help maximizing mixing performance.
Layering isn’t the only factor impacting mixer performance. The vertical mixer design, operating speed and condition of the knives all influence mixing performance. You must be able to identify when the maximum life of the knives has been reached for optimal performance.
Do more with less
With labor shortages remaining a challenge, saving time with lean farm management presents a real opportunity.
“For a lot of agricultural entrepreneurs, ranchers or farmers, the pursuit of waste reduction allows them to do more with less labor,” said Core.
Contact your Vermeer dealer to discover how a vertical mixer can improve your feed lot efficiency.
Information noted above was gathered from a third party who was advised his/her experience might be featured in marketing materials. This article contains third-party observations, advice or experiences that do not necessarily reflect the opinions of Vermeer Corporation, its affiliates or its dealers. Individual results may vary based on care and operation of machine and crop and field conditions, which may adversely affect performance.
Vermeer Corporation reserves the right to make changes in engineering, design and specifications; add improvements; or discontinue manufacturing at any time without notice or obligation.
Equipment shown is for illustrative purposes only and may display optional accessories or components specific to their global region.
Please contact your local Vermeer dealer for more information on machine specifications Vermeer, the Vermeer logo and Atlas are trademarks of Vermeer Manufacturing Company in the U.S. and/or other countries. © 2023 Vermeer Corporation. All Rights Reserved.