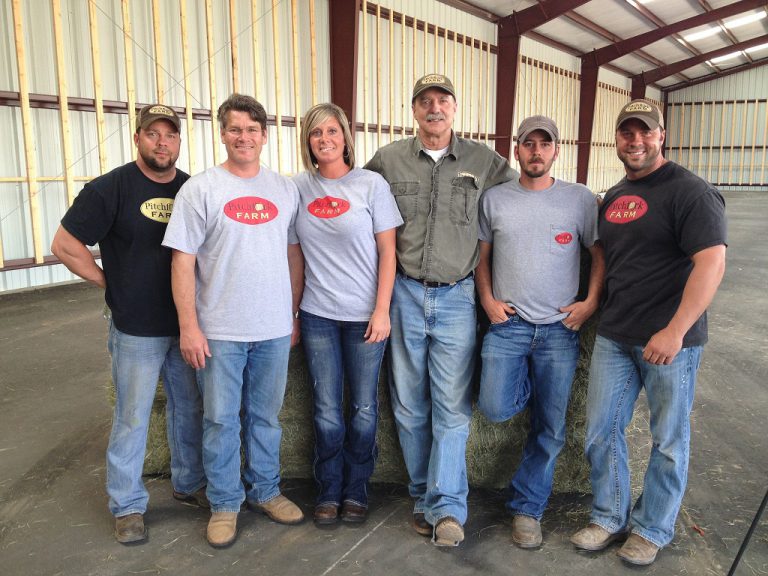
No Time to Waste
February 2016
With 200 acres of Bermuda grass that he and his crew cut and bale every 28 days from late May through the end of September, Mark Pretti counts the local weatherman as one of his greatest allies. However, as manager of Pitchfork Farm near Somerville, Tennessee, Pretti also relies heavily on two Vermeer TE330 tedders and a Vermeer R2300 twin rake to help manage the crop once it has been cut.
“My theory is the faster you can get it cut down and the faster you can get it baled, the better the hay quality,” said Pretti, who has been the farm manager at Pitchfork Farm since 2008. “So, we’ll use two mower conditioners to cut around 40 acres at a time in about four to five hours. Then, depending on the time of day and weather, we’ll come in right behind the mowers with the two 33½-foot Vermeer tedders and ted the crop at least once, and often twice, that same day.”
Pretti says it will be three days from the time the crop is cut until it is ready to bale, which means the hay is tedded at least once or twice a day each additional day the crop lays on the ground – up to a total of five or six times. The whole idea is to facilitate faster and more even drying.
Under Pretti’s management program, there’s a lot of hay to dry, too. It starts with Vaughn Bermuda, which is a leafy, warm-season grass variety with excellent nutritional value that is well adapted to the soils, climate and weather conditions in west Tennessee.
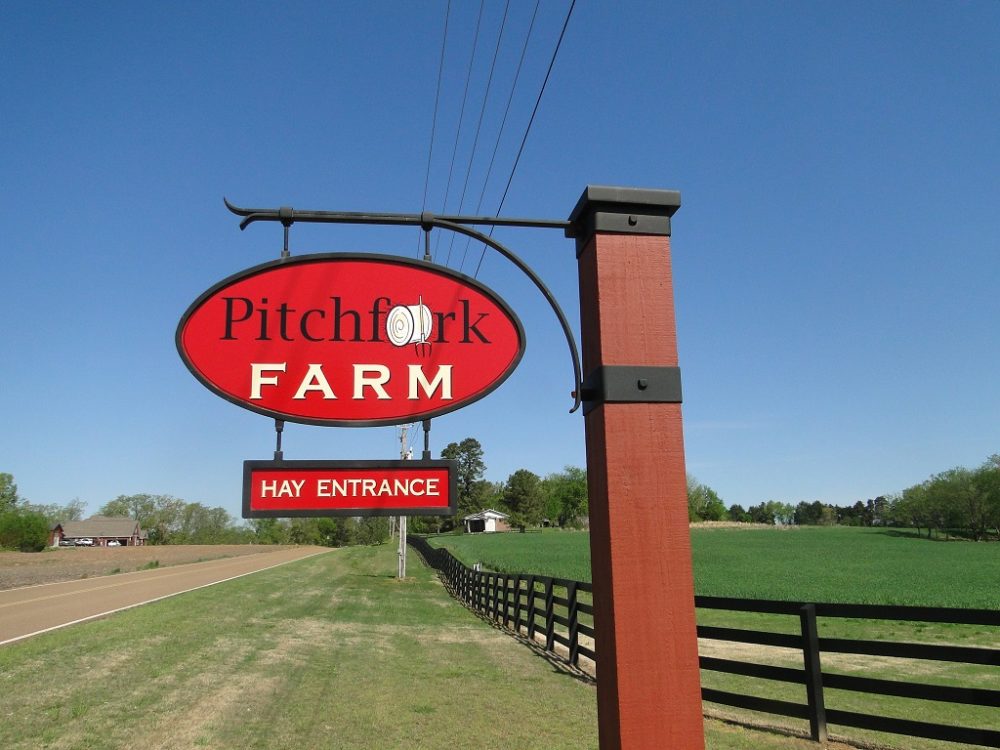
In addition, all the hay fields are under center pivot irrigation so Pretti doesn’t have to worry about drought or stress on the crop during hot weather. Finally, the production team, which includes Pretti, his two 38-year-old twin sons and one additional employee, applies a special blend of nitrogen, phosphate and potash after each cutting and supplements that with additional nitrogen applications through
the pivots.
They also conduct soil tests each year, aerate fields each spring and grid sample fields every three years. As a result, the farm typically produces an average of 93 plus small square bales per acre, per cutting. In 2014, that added up to sales of around 100,000 bales.
“Last year, we sold right at 60,000 bales,” he recalled. “However, we took 110 acres out of production at the end of the 2014 season and we just put 60 acres back into Bermuda this past spring.”
As Pretti explained, virtually all the hay that Pitchfork Farm produces goes to the equine market, which includes owners, horse farms and racetracks throughout the country. Hence, the need for quality hay that is free of weeds, debris and foreign material.
“One of the main reasons I switched to Vermeer tedders was because we were always losing teeth on the tedders we previously used,” he said. “Unfortunately, we never knew where a lot of the broken teeth went,” he added, expressing the ever-present fear that a lost tine might go through the baler, end up in a bale or, perhaps, puncture a tire. “In contrast, I’ve now used one of the Vermeer tedders for two seasons and the other for three seasons and never yet lost a tine.”
He also related that the unique “hook tines” on Vermeer tedders rotate the hay for better dry down consistency. In addition, the large-diameter rotors operate at lower revolution speeds, which helps prevent crop loss and allows longer grasses and heavier lumps to separate and fan out more evenly.
“In the meantime, we’ll adjust the windrow size created by the mower conditioners to match weather forecasts,” he explained. “If the prediction is for several days of sun and warm weather, we’ll make the windrows as wide as possible so they can start drying. However, if the forecast calls for a chance of rain, we will often make a narrower windrow so that in case it does rain, the soil on either side of it will dry faster so we’re not tedding hay onto wet ground.”
"One of the main reasons I switched to Vermeer tedders was because we were always losing teeth on the tedders we previously used."Once the crop has dried to the proper moisture level, Pretti and his crew rake the hay into large windrows that keep their two small square balers running at peak capacity. “I used to run another brand before purchasing the Vermeer R2300 last year,” he said. “With the other machine, we generally had to make two passes to get a windrow as large as we wanted it. However, with the R2300, we can make the perfect windrow in one pass, which means the baler operators aren’t catching up with the rakes and having to sit and ‘twiddle their thumbs’.”
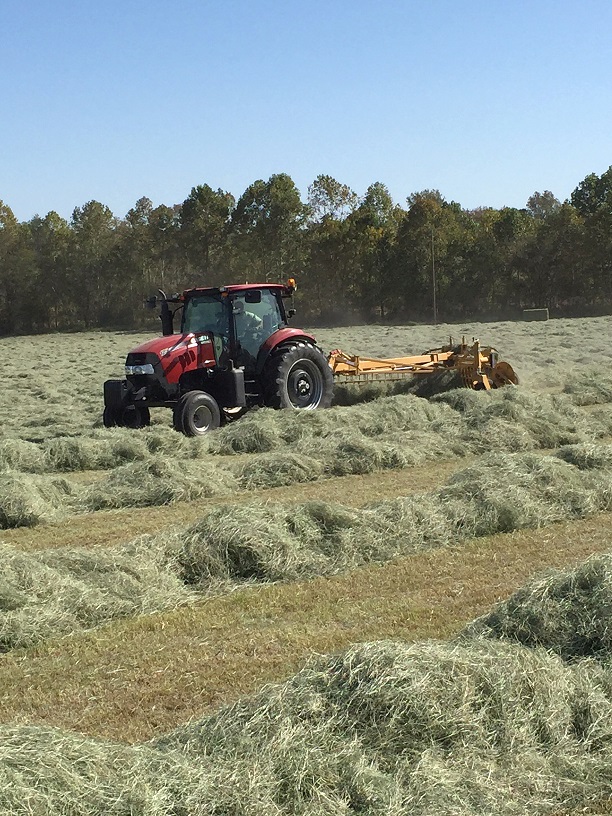
While gathering 23 feet of crop into one windrow, Pretti is able to also adjust both the width of the windrow and the raking action to match the field and conditions. Once the crop is baled, Pretti once again turns to specialized equipment — this time to eliminate the labor typically involved with handling small rectangular bales.
Instead of manually handling the 50-pound bales, Pitchfork Farm uses a Bale Baron machine to bundle the 14-by-18-by-34-inch bales into a package that measures 35-by-54-by-92 to 94 inches and contains 21 bales.
“In most cases, a bale is only handled two or three times between the time it is baled and shipped,” he explained. “Because we can handle the bundles with a skid steer loader or tractor loader, they’re moved straight into the barn for storage. It’s the same situation when we load them onto a truck. By moving 21 bales at a time, we can fill a 53-foot cargo van semi trailer with 693 bales in about 20 minutes.”
These days, however, the team doesn’t have much extra time on their hands. In addition to the 200 acres of hay, Pitchfork Farm incorporates about 1,500 acres of row crops, which until last year were custom farmed by other farmers. However, management has since decided to farm the row crop acreage, as well, which means that in addition to cutting, tedding, raking and baling hay, they’re now faced with planting, managing and harvesting several hundred acres of corn and soybeans. That means there’s no time to waste.
Fortunately, their Vermeer TE330 tedders and R2300 twin rake have put a little more time back on their side.