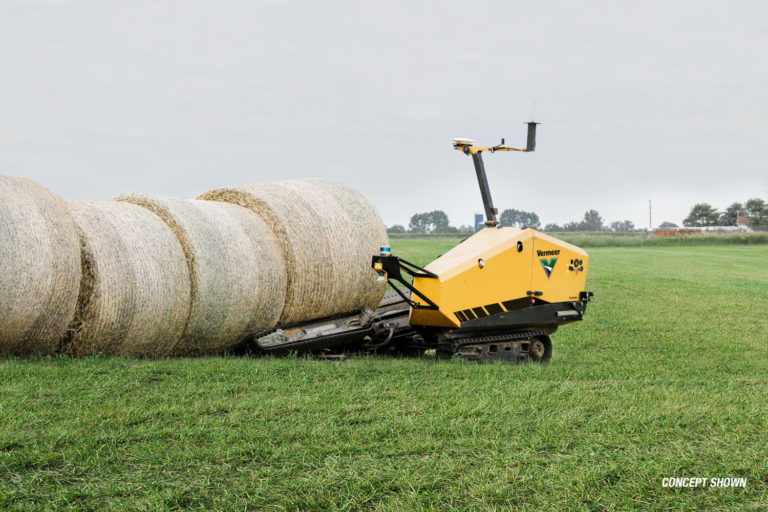
Vermeer forage innovations address agricultural labor challenges
July 2021
Finding and retaining qualified, skilled labor — and maximizing your productivity in the field — are universal challenges all types of agriculture producers face. Time-consuming practices and agricultural labor challenges are some of the reasons behind a line-up of new forage innovations coming from Vermeer. These advancements build on a storied history of innovation at Vermeer, which is celebrating 50 years of its large, round baler — an innovation that changed the way hay and forage producers feed and fuel the world.
“Our team is dedicated to developing practical ways to help forage producers make the most of their available labor and get the most out of their time in the field,” said Vermeer Research and Development Manager Kent Thompson. “Our team works to identify solutions that producers don’t even realize are possible, all focused around their hay operation.”
Autonomous bale mover
Will autonomy be coming to a hay field near you?
The entire haymaking process is all about time. It’s not only important to cut, ted, rake and bale hay at the right time and moisture level, but producers also need to haul and store bales in a timely fashion to help the next crop start right. What if an autonomous machine could take care of one of those mundane and time-consuming steps for you?
The new autonomous bale mover concept at Vermeer is designed to help producers reduce the need for labor to move bales from where they’re dropped in the field to the field’s edge or a storage area. The machine will travel around the field autonomously via a suite of onboard sensors to locate bales, confirm their location, pick them up and move them to a predetermined location. As a result, the machine can completely eliminate a labor-intensive step of the haymaking process — moving bales to a location where they can later be transported to a buyer or storage area on the farm.
“The autonomous bale mover knows where it is relative to the bales. It will develop a route and can pick up to three bales at a time. Once full, it will determine its best path back to a predetermined location to unload bales,” Thompson said. “With this machine, producers can eliminate the final step of moving bales manually.”
Thompson added the Vermeer Forage Solutions team is working through optimal scenarios for how the autonomous machine will work in the field.
Vermeer believes one benefit of the autonomous bale mover concept is to someday allow operators to monitor the autonomous bale mover from a remote location, allowing them to be doing other jobs at other locations or take a well-deserved rest, while the machine picks up bales. The net effect is a way to help overcome the growing agricultural labor challenges producers face.
Onboard bearing temperature sensors
A new way to keep an eye on predictive maintenance
A failed bearing on a baler can take time away from the field and cost more in replacement parts. Plus, it never seems to happen at an optimal time.
That’s the objective of another forage innovation in development at Vermeer — the onboard bearing temp sensors are a wireless, battery-powered heat sensor that can help operators monitor baler bearing temperatures from the cab. This information can help prevent unexpected bearings from failing due to contamination or from reach their end-of-life.
“This is a preventative maintenance innovation. The sensors will alert operators when bearing temperatures are rising. Operators can monitor the temperature from the cab and decide if they can finish the field or if they need to stop immediately,” said engineer for Vermeer forage innovations Nathan Dockter. “When given this information ahead of time, operators can order new bearings and replace them before failures happen, which helps prevent time out of the field.”
Normally, baler bearings don’t fail immediately; it’s a gradual process. But by being able to keep an eye on operating temperatures, operators will be equipped to replace bearings before they reach the end of their life or fail.
“These sensors will help paint the picture of how dealer service technicians can recommend maintenance based on temperature and take care of these issues during regularly scheduled maintenance,” Dockter said.
Automated baling assistance technology
Autosteer for self-propelled baling
Precision agriculture tools common in row crop equipment have traditionally been absent in the forage sector. Not anymore. An upcoming forage innovation will deliver what Thompson said is essentially an autosteer-type of guidance system for the popular Vermeer ZR5-1200 self-propelled baler. “The ZR5-1200 was the first of its kind when it was introduced back in 2017 and forever changed the way hay can be made” said Thompson, “but our team isn’t finished innovating it yet.”
The automated baling assistance technology will use a light detection and ranging (LiDAR) sensor to visually track the windrow, and once the operator enables the automated baling assistance technology, it will steer the machine. Unlike autosteer, this technology does not use GPS or RTK, rather uses sensors to help the self-propelled baler track and follow the windrow, and steer the machine.
“It’s an automation program, not an autonomous innovation, so there’s still an operator in the cab. The technology will allow the ZR5-1200 to accurately follow the windrow and, in the future, compensate for crop variances in the windrow. That way, drivers can still operate the machine or move it around, if necessary, to optimize the uniformity of the crop going into the pickup and therefore the shape of the bale,” said Vermeer senior systems engineer for forage innovations Gary Burns. “Its automation is intended to help meet the growing need to produce good-looking square-shouldered bales.”
When it becomes available to the public, there will be specific labor benefits to the system, namely for operations, that will reduce the learning curve of less-experienced operators to make consistent bales. “This automation can allow the operator to make good-looking bales all day long,” Burns added.
Forage Commander App
There is an app for that
In today’s era where there are apps for everything, from online banking and grocery shopping to managing your farm fleet and keeping track of your cattle records, the Vermeer
team believes there’s an opportunity to have an app for making hay. The Vermeer Forage Commander app, currently being tested by the team, is designed to collect and manage field data produced by balers and give producers a new way to track their progress and productivity.
“This app is really designed for an operator who wants to either better understand their productivity in the field or for a producer who is looking for a more convenient tool to help with their custom hay operation,” said Vermeer Product Manager Shawn Wang.
The app will connect via Bluetooth to the data gateway unit located on the baler. Whenever the user’s smart device is within range of the baler, it will automatically sync to provide the latest information. By tracking field and cutting data, the app will let producers see a wide range of field statistics, such as bales per field, bale weight (if scale is equipped), average bale moisture (if moisture is equipped), bales per hour and more.
Ideal for helping custom operators streamline their work, all the data can be paired with the customer manager widget of the app that keeps the information sorted by customer and field. The baling data and customer information will allow Forage Commander to generate an invoice directly from the app that can be emailed to the custom operator’s customer. Producers can also manually enter other custom work (hauling manure, for example) on the invoice and even charge at their pre-defined rates by job.
There’s no set timeline for market readiness of these three innovations, but stay tuned for the latest updates by subscribing to the Makin’ Hay e-newsletter.