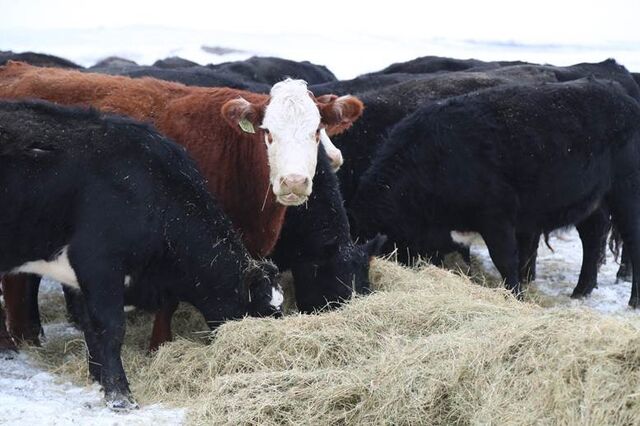
4 Tips for Keeping Your Herd Productive Over Winter
August 2023
With shifts in the weather come shifts in herd management priorities. You should begin developing your plans for wintering your herd and identifying lower-performing cull cattle before cold weather arrives.
Denise Schwab, Iowa State University Extension beef specialist for northeast Iowa, said there are a few things for beef cattle producers to keep in mind as the seasons change. In her more than 40 years of experience, she’s learned decisions regarding winter on the farm hinge on the weather, available feed resources and culling criteria.
“The weather, the stored feed, the fact that herd requirements are going up because of gestation … That’s what makes winter feeding our most challenging and expensive feeding period,” she explained.
1. Consider your costs.
Regularly evaluating input costs ensures agricultural businesses can stay productive for years to come. You can determine where gains can be made by assessing every component of the business from equipment to herd culling.
“You need to know your cash costs,” Schwab said. “That’s what you write a check for. And of those cash costs, feed is our biggest expense.”
In fact, 50% to 60% of production costs are attributed to feed while the rest can be found in veterinary, repairs, labor, insurance and other miscellaneous expenses.
Schwab cautioned producers against ending their financial evaluation there, though.
“It is important to be able to answer the following questions to have a clear management plan,” she said. “Why are we raising cattle? What are our objectives? What is our actual production cost? Then look at storage, feed waste and losses to make sure we do everything we can to minimize those.”
She noted there are non-cash costs at play, as well.
“That would be things like depreciation and changing value on the cow herd,” she said.
Ongoing expenses, however, can be found in the tractor maintenance for hauling hay and spreading manure, the manure spreader, feed wagon and pickup — plus the fuel to operate them. A good accounting system with the ability to track both can help.
Bottom line, Schwab says most beef cattle herds have between $800 and $1,000 per head annually in input costs. That means calves should bring more than that to remain profitable, and cattle producers can’t afford to keep around cull cattle.
2. Cull nonproductive cattle.
In the spirit of increasing business productivity, Schwab said producers can’t have a sustainable business by feeding open cows. With this in mind, she encouraged pregnancy checking early and culling cattle that did not rebreed on time.
“We’ve got to cull open cows earlier before we get into our winter-feeding timeframe,” she said.
Other culling criteria may come from an evaluation of structure, docility, performance, teats and udders.
“Culling is absolutely important,” she said. “Especially since most of the country, or at least most of cow country, has been in dry conditions for the last two or three years. When feed supplies are tight or really expensive, those problem cows need to find a different home. We need to look at how we can do that as well to help stretch our feed supply.”
After the initial culling of open cows, Schwab says the next step is to evaluate weaning weights. For example, you could ship the bottom 5-10% of cows that weaned the lightest calves that year. If you do that yearly, the average weaning weight will begin to increase , just watch that mature cow size doesn’t increase too much as well.
Once the herd is free of nonproductive cattle, maintaining condition on the remainder of the herd comes center stage.
3. Maintain body condition scores.
A cow’s body condition throughout the winter months plays a huge role in productivity of the herd through gestation and her ability to rebreed in a timely fashion later — and avoid the cull pen.
“The body condition scores of the cows are going to drive everything on our feeding program and our costs,” Schwab said.
She recommended cows be at a six at calving to help them return to estrus sooner. Because it is easier to maintain body condition than to increase it, Schwab said to have cattle at the target going into winter and consider culling those that are not. This prevents a need for extra feed to get them there during one of the hardest times of the year.
To keep up with nutritional requirements, producers should consider storing hay and forage ahead of time. Historically, the general rule of thumb has been to have about two and half tons of hay per cow per year, but varying environments and waste hold some bearing on that figure.
4. Have a feed management plan.
Producers can prevent storage waste by protecting their feedstuffs. Some examples Schwab offered were getting hay off the ground with pallets or gravel and covering it with a tarp or storing it in a barn. These minor changes can shift losses from 25% to less than 5%.
“Storage loss is part of it, and then feeding loss is something else we need to pay attention to,” she said.
That is where the BPX9010 bale processor, a feed wagon or a vertical feed mixer can help. Investing in these pieces of equipment helps high-quality, consistent feed to be delivered to livestock with minimal amount of waste.BPX9010
Additionally, cover crops or crop residues may be viable options to extend feed resources throughout the winter for cattle who made it past the culling criteria. Because cattle nutrition can be regionally specific during the winter months, Schwab recommended referencing your university extension systems as they often have a good set of resources about cow-calf nutrition, feed, hay management and forage management.
Before winter hits, be proactive and create a management plan with these tips in mind. Taking the time now offers producers the best chance at long-term gain over the winter months and beyond for the cowherd.
Vermeer Corporation reserves the right to make changes in engineering, design and specifications; add improvements; or discontinue manufacturing at any time without notice or obligation.
Equipment shown is for illustrative purposes only and may display optional accessories or components specific to their global region.
Please contact your local Vermeer dealer for more information on machine specifications.
Vermeer and the Vermeer logo are trademarks of Vermeer Manufacturing Company in the U.S. and/or other countries.
© 2023 Vermeer Corporation. All Rights Reserved.