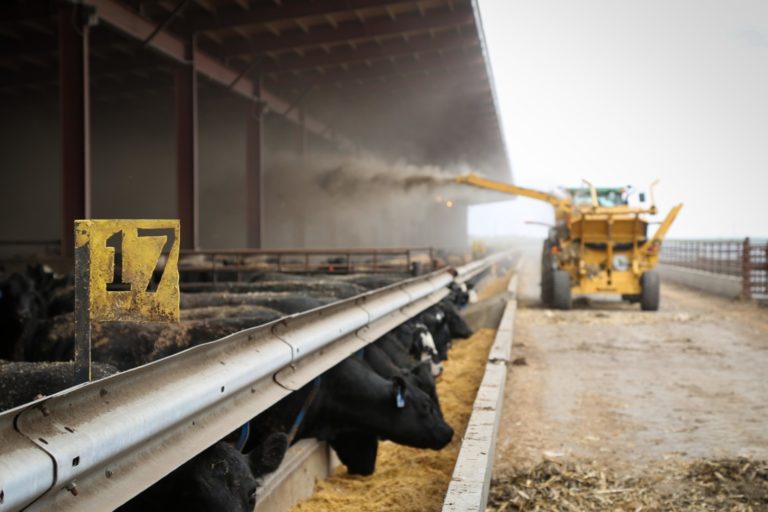
Does a Bale Processor Make Sense for Your Livestock Operation?
February 2018
For many years, livestock producers have embraced the use of bale processors for a lot of different reasons. However, there are very few studies that have evaluated them with a cost analysis in order to track the value they provide to owners.
Frankly, it’s not always easy to quantify the amount of time that’s saved, the waste that is eliminated and the operating efficiencies that are realized when it involves a piece of equipment designed to multitask for a variety of different functions.
The real answer to, “Does a bale processor make sense for your livestock operation?” probably depends what you hope to get out of it by the way you use and manage it in your operation. So let’s start with what we do know and what many owners and operators have told us.
When you visit with owners and operators, one of the biggest reasons they prefer processors is the versatility it gives them. For example, the ability to process everything from hay to cornstalk bales; the ability to process round bales or square bales; the flexibility to perform all kinds of tasks – laying down windrows in the field, bunk feeding, right-sizing hay material for total mixed rations, blowing bedding into shelters or forage into storage bunkers.
Or even repurposing it as a different type of tool and making it a new profit center – such as contracting out your services to developers and contractors in land reclamation projects. In other words, using your processor to distribute a consistent layer of straw to reduce erosion and reclaim land in new commercial and residential developments, or along roads and interstates.
Another reason? Processing hay makes marginal hay more palatable and average hay better. Why? Because it helps effectively eliminate most of the dust, mold and mildew that accumulates in a bale before the hay enters the digestive systems of your cows; and it reduces the amount of sorting, waste and manure that typically takes place around the feed ring.
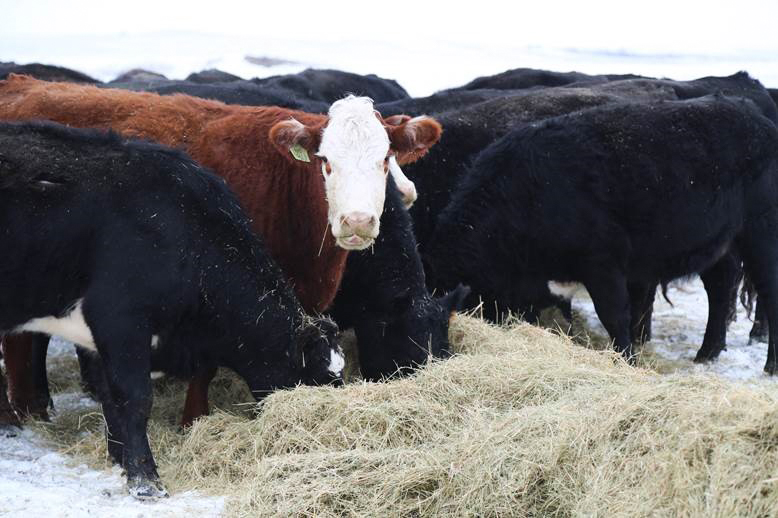
From a feeding and bedding standpoint, it’s a much easier, faster and more efficient way to distribute your hay, especially during the middle of winter.
Operators have the ability to control and monitor consumption by processing and windrowing bales in the field (compared to simply unrolling them in the field), cows consume more hay and waste less. In fact, studies conducted in 2011 by three universities demonstrated a 16-pound weight gain advantage during a 60-day feeding period.
Of course, the biggest factor of hay waste still happens during storage. Studies have found an average dry matter loss of 28 percent for hay stored outside without a cover. When hay was stored outside and covered, the loss dropped to 13 percent, but hay stored in a building reduced the loss to about 5 percent.
Average waste for either ground feeding method was about 18 percent, but feeding in some type of structure was about 5 percent. However, this advantage is offset by the buildup of manure around the feed ring and the limited access some cows may have in finding a spot at the “table.”*
Do you prefer the economy and flexibility to process and mix your own feed rations and the freedom to do it according to your schedule versus that of an outside supplier?
Some processors can now be equipped with a final cut option, which includes an additional cutting stage to further reduce processed hay down to the optimum precut material size for better digestibility and feed efficiency in a cow’s rumen. This reduces the average cut length down to 2 to 4 inches before it enters the TMR.
If you’re still interested, what kind of processor should you look for?
Today there are two basic styles of bale processors. Both feature a similar rotor design for processing the bale. The primary difference between the two is how the bale is handled and turned in the tub. One style of processor uses a dual feed-roller design with staggered, adjustable rollers.
In contrast, the most popular processor design incorporates a simpler slat-and-chain bed. This creates a more consistent, user-friendly system when feeding the bale, because the slats are constantly engaged and in contact with some part of the bale. This design also avoids the hassle of twine buildup, which is fairly common with the dual feed-roller concept.
Horsepower is a crucial factor that should always be considered when comparing models. If the bale is sluggish going through the processor it can pull the tractor down, bringing production to a screeching halt. There’s nothing more frustrating than dealing with a plugged processor (particularly during the cold winter months).
You will find that processors built to handle sufficient horsepower tend to generate a more even and consistent feeding action to the rotor. This equates to fewer performance issues and typically requires less fuel to operate.
There is no definitive answer to the question, “Does a bale processor make sense for your livestock operation?” The needs of each operation vary, so it’s important to evaluate what you really want to accomplish. Look around your operation and consider the possibilities – then ask your dealer for a demonstration.
*Based on studies conducted in 2011 by North Dakota State University (NDSU), the University of Minnesota (UM) and Michigan State University (MSU).