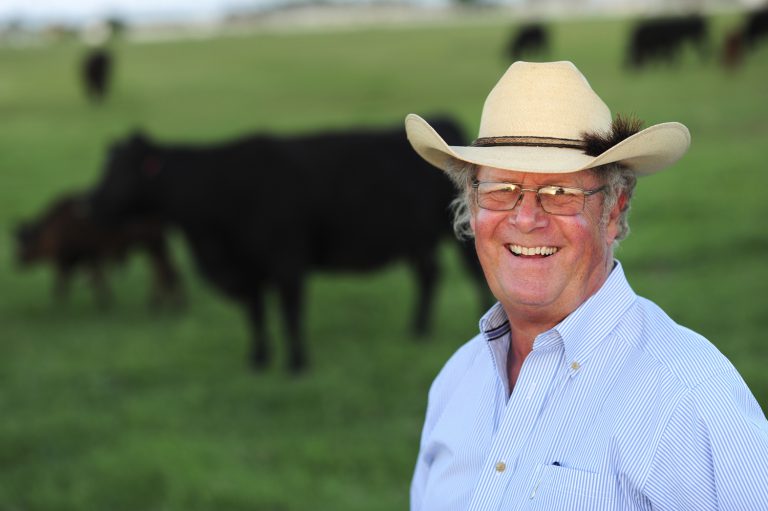
Unexpected Necessity
February 2015
If anyone were to have asked him last fall, J. Mack Bohn would have admitted that his reasons for purchasing a new Vermeer BPX9000 bale processor were to help reduce bale waste and to get the tax credit before the end of 2013.
“It was a legitimate investment at the time,” he insisted. But when neighbors ask him now why he bought the BPX9000, he says “It’s for reasons I didn’t even know about at the time.”
As the owner of Diamond JK Ranches, based near Cyril, Oklahoma, Bohn is like most other cattlemen in that he traditionally has to provide the herd with hay during the winter months. However, five years into one of the region’s worst droughts, Bohn is buying hay on a regular basis and providing supplemental feed through much of the year to supplement his pasture forage.
It’s not like Bohn can reduce the size of his herd in response to the drought, either. Following years of genetic and DNA testing, embryo transplants and selective breeding, Bohn has developed a highly reputable breeding stock program. While much of his program revolves around a purebred Brangus herd, his most recent accomplishment has been the development of his own line of UltraBlack bulls and cows. UltraBlack animals are 3/16th Brahman and 13/16th Angus.
Although Bohn sells both bulls and cows to a number of his long-term clients, he also provides breeding stock to three other ranches in northwest Oklahoma, Kentucky and Texas.
“If I was just raising commercial cattle, I’d be bored to death,” said Bohn. “I have to have a mission and I’m always trying to stay out in front,” he added. “I had a friend once tell me ‘If you don’t get out in front of the pack, the view never changes.'”
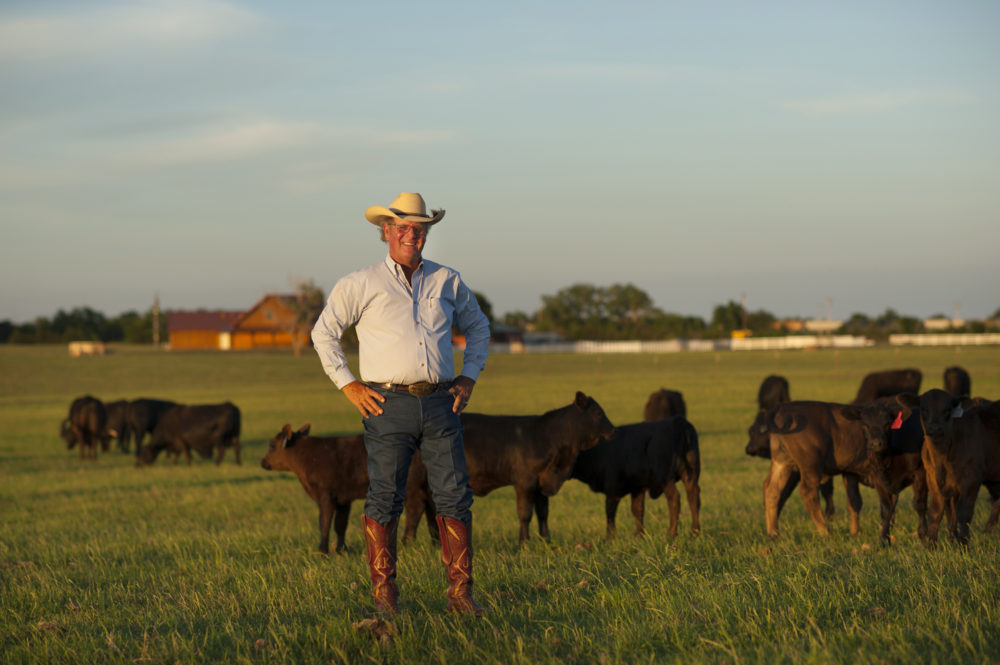
Consequently, Bohn isn’t afraid to try something new or to be the pioneer. That was indeed the case with his purchase of the Vermeer BPX9000 bale processor. Bohn’s was not only the first Vermeer bale processor in the area, but he ordered it with all the options, including the optional scales and the ability to process square bales in case that becomes necessary.
“A lot of people look at the scales as an unnecessary luxury,” he said. “I’ll admit, we got pretty good at estimating how much the cows would eat in a day and rolling out the right amount. But I don’t think anybody can look at a round bale and tell you within 200 pounds what it will weigh. With the scales, we can put out exactly 35 pounds per cow, and if they don’t clean it all up, we can cut it back a few pounds per day. After using it, I wouldn’t buy a bale processor without it.”
While Bohn admits the latest bale processor from Vermeer does reduce bale waste by shredding and mixing hay into more palatable windrows, he says he has since learned that it does so much more.
“Our feed trucks are already equipped with beds that can unroll round bales, so that in itself offers a savings over round bale feeders,” he explained. “However, the width still creates an environment that’s comfortable for cows and calves to bed down on, and that just creates a breeding ground for bacteria,” he added, noting that he would still feed in a different area each day. “We have spring calves and fall calves, which means the fall calves are going to be with their mommas through the entire winter when we’re feeding on the ground.”
However, once the hay is processed with the BPX9000, it is placed in a windrow that is too narrow for any cow to comfortably lie down on. That leads to a cleaner environment and less illness. Better yet, Bohn said the windrows are deposited on the ground with such force that they don’t move.
“Down here, the wind is always blowing,” he said. “So it wasn’t unusual for a 40-mile-per-hour wind to pick up the edge of the hay we’d unrolled and scatter $70 worth of Bermuda across the pasture. So we’re saving hay there, too.”
One of the things that has surprised him the most, however, is how clean and palatable the hay is after going through the processor. Bohn said it starts by setting the unit so it removes any twine or netwrap from the bales.
“I don’t like my cows eating plastic, even though I equally hate the job of cutting netwrap off of the bales,” he insisted. “This BPX9000 cleans the bales so well that you can hardly find a scrap of netwrap in the windrow. Sure, you have to cut it off the rotor every two or three days, but that’s only about a 15-minute process.”
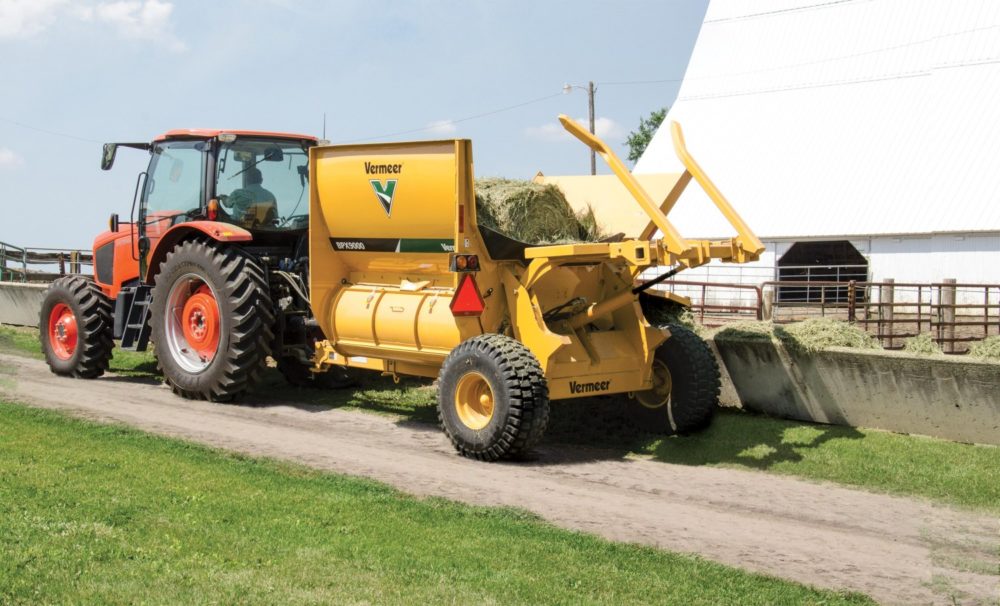
“In the meantime, you wouldn’t believe how much dirt there is in a bale,” he continued. “The guy I buy my hay from is one of the best in the business, yet the dust is so thick at times you can barely see the processor. That’s dirt the cows aren’t eating.”
An even more valuable benefit, he added, is the fact that the calves start eating hay just as soon as their rumen develops, simply because it has been processed into a more palatable form. That means both cows and calves are better conditioned.
“The BPX9000 won’t perform miracles and turn bad hay into good hay,” Bohn related. “No bale processor can do that. But it will make good hay into better hay.”
“I’m certainly not one to hold back an opinion about something, which sometimes rubs people the wrong way,” he admitted. “But it’s hard to find anything to complain about with this machine. It’s gone from being a tax deduction and somewhat of a luxury to an essential piece of equipment.”