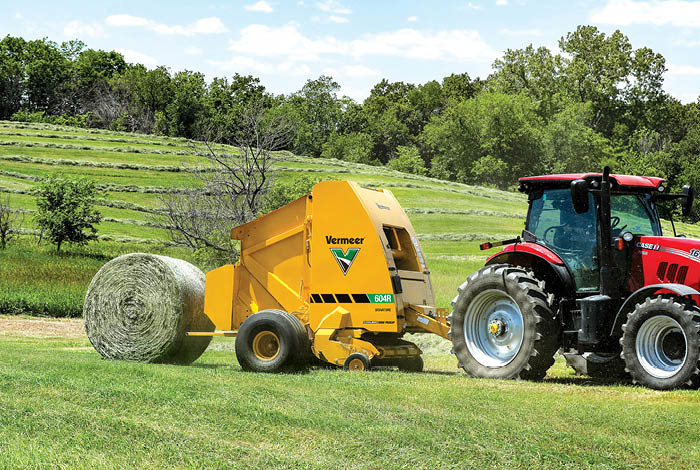
Do Appealing Bales Mean Quality Hay?
October 2024
When it comes to round hay bales, looks aren’t everything. But a well-made bale has benefits — like better storage capabilities and customer appeal.
Matt Stanley understands the relationship between quality hay and bale appearance. As both a producer and a Vermeer regional service representative, Stanley has seen just about every side of the hay industry. He knows the power of appealing bales. He also knows looks don’t tell the whole story.
“You can make junk hay look very good in a bale. If you can make it stand tall and cover it in a netwrap, you can sell it,” he said. “That’s the marketability problem with a good-looking bale. You can hide a lot of stuff in a good-looking bale of hay.”
So, if bale appearance doesn’t always indicate quality, why should producers bother with perfecting their baling process?
A good-looking bale is a strong bale
Sure, cattle and horses probably won’t turn their noses up at a poorly made bale. But cattle producers and horse owners just might. They know quality hay bales are dense and tightly wrapped, offering two advantages.
First, there’s stackability. Strong, square-shouldered round bales are easier to stack (and transport). That’s less hassle for customers as they move bales around their operations. Second, dense bales offer protection against the elements. As a result, hay from well-made bales can often last longer without significant spoilage compared to less dense bales.
However, bale appearance right after a bale is formed can be deceiving. Stanley encourages producers to keep an eye on how it holds up.
“The main thing about a good-looking bale is, it’s not all about what it looks like when it comes out of the baler,” he said. “I want to come back in two or three weeks and still see it standing in a perfect circle. One that doesn’t allow air to get inside that bale to keep drying the hay out and doesn’t allow moisture to get inside that bale.”
Every step matters for quality hay bales
The process of creating good-looking, strong-shouldered bales starts long before the baler comes out of the machine shed.
“The best-looking bale you can make starts when you have your rake set perfectly, and you can rake a windrow that’s just even on both ends,” he said. “It’s good and tall, and you run that baler right through it. The bale comes out completely flat across the top. It’s got square edges with netwrap that goes out to the edge.”
Stanley’s approach starts with a good, clean cut in the field. If he brings out the tedder, he makes sure it scatters the grass well, so it has room to breathe. However, he believes the tedding process is forgiving. According to Stanley, there’s no wrong way to ted — as long as a producer adjusts the settings so it can pick up all the hay.
Then the rake comes in — one of the most important pieces of equipment in the baling process. Because well-formed windrows are essential for well-made bales. Producers must check settings and consider best practices before taking the rake into the field. The windrow width should match the bale chamber width. Once in the field, a ground speed of 7 mph – 10 mph (11 km/hr – 16 km/hr) is usually ideal to minimize contamination and protect the rake tines.
“We’ve got to make sure that rake is in the optimum performance stage, and then we can make our baler perform at optimum performance,” Stanley said.
Once the hay is ready for baling — Stanley recommends the 12% to 14% moisture range for high-quality hay — producers can make final adjustments to the baler. For Stanley, this means examining the netwrap setup before rolling even one bale.
“Whatever baler we’re looking at, the very first thing that I’m going to dial in is the netwrap,” he said. “I’m going to walk to the back of the baler, open the netwrap door, and I’m going to see how it’s timed, how it’s set, how tight the break is, and if I don’t like it, then I’m going to start doing my adjustments on it.”
Then, Stanley looks at baling speed. He favors a slower approach, maxing out around 480 rpm. He believes it results in better bales. And finally, his operation makes sure windrows are matched to the baler — not too wide, not too narrow.
Small adjustments can have a big impact
While there are plenty of ways for producers to experiment with baling changes, they don’t have to work alone. Stanley believes producers can learn from each other and make improvements along the way.
“If I see someone’s hay down the road and their netwrap looks way better than mine, I’m going to ask them what they did differently,” he said. “As producers, we don’t ask enough questions, because most of the time, there’s an essence of time that we are allowed.”
He also reminds producers how valuable an equipment operator’s manual can be. According to Stanley, producers can find many of the details they’re looking for in those pages.
Vermeer dealers are also experts in hay and forage, offering support in the field. They’re available to help with questions, equipment adjustments, maintenance and service. Find your dealer today.
Vermeer Corporation reserves the right to make changes in engineering, design and specifications; add improvements; or discontinue manufacturing at any time without notice or obligation.
Equipment shown is for illustrative purposes only and may display optional accessories or components specific to their global region.
Please contact your local Vermeer dealer for more information on machine specifications.
Vermeer, the Vermeer logo and the Black, White, Green bale wrap color scheme (Vermeer Net) are trademarks of Vermeer Manufacturing Company in the U.S. and/or other countries.
© 2024 Vermeer Corporation. All Rights Reserved.